The suspension of a car undergoes severe tests by Australian roads daily. According to statistics, the suspension elements – silent blocks, various ball joints, shock absorbers, etc. – are the most popular spare parts. Unfortunately, when installing new car parts, inexperienced mechanics and car enthusiasts often make typical mistakes that lead to a quick failure of the new car part. Today, we will analyze some of them and tell you how to do it and how not.
Silent blocks
Rubber-metal hinges (silent blocks) connect suspension parts and fasten the suspension to the body. In the installation process of the silent blocks, the following mistakes often occur:
1. The original seat has not undergone prep work. The seat of the silent block in the lever/steering knuckle/on the body must undergo preparation for the installation of a new part. Preparation includes a thorough cleaning, geometry check (to avoid ovality or loose fit in a broken hole), and lubrication.
If the seat is dirty and has lost its geometry, the installation of the silent block will become skew. Which will lead to incorrect operation and quick failure. A dry fit can worsen the wear on the seat, as well as seriously complicate subsequent disassembly.
2. The silent block requires installation on the unclenched suspension/not according to the marks. Asymmetric silent blocks with cavities and special geometry of the rubber filler require to be on the correct orientation relative to the lever or rod before pressing. Levers can be labeled, in other cases, please to refer to the automakers manual. All silent blocks must be finally tightened, only after lowering the machine on the wheels so that the suspension takes its working position.
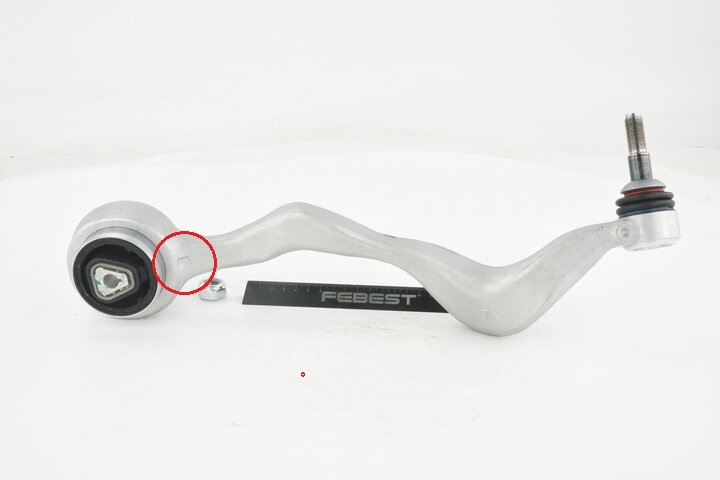
Silent blocks tightened to the final moment with the wheels hanging out, will be constantly loaded, and the rubber filler will be constantly twisted. This will cause disastrously rapid wear of even the highest quality rubber-metal joints.
Stabilizers pole
When replacing the pits, mistakes can happen that lead to rapid wear.
1. Reupholsterey of single-hinged racks. The stabilizer struts are attached to the body through rubber cushions must be protected from overtightening. The rubber can become flat and then tear if the torque is exceeded, and it is useless to use a torque wrench due to the rubbers ability to deform. Use the manual, where the number of turns is indicated, or the mounting dimension for tightening single-hinged racks.
2. Wrong orientation of racks. Many models of double-hinged stabilizer struts are asymmetrical. With a separation of parts for the left and right sides of the car. If neglect occurs and the sides are confused, then the ball pins of the racks will immediately find themselves in extreme positions. The same partly applies to single-hinged struts. When tightening the upper nut, it is necessary to protect the strut from turning, otherwise the ball pin will be unnecessarily turned out.
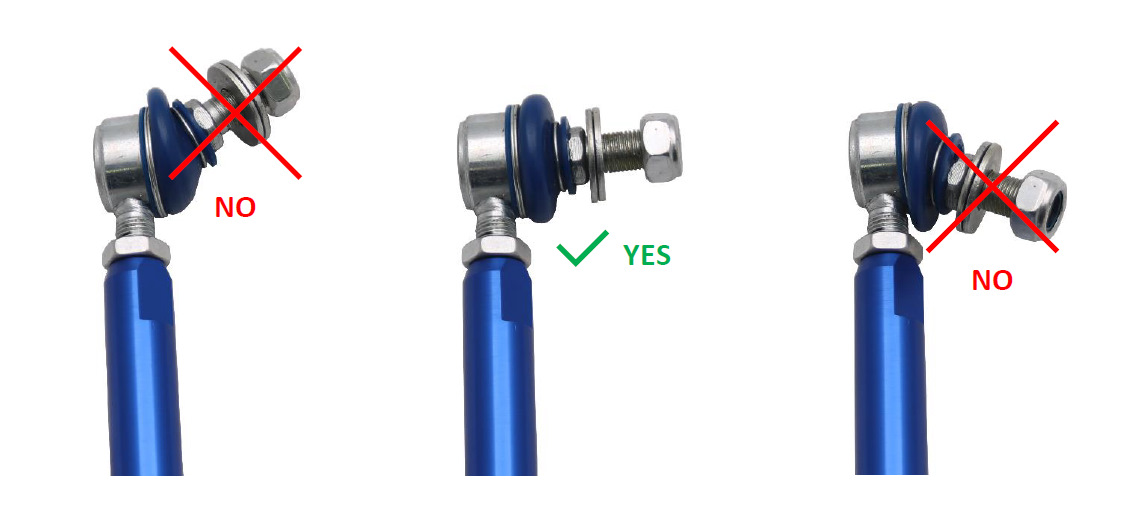
With a compressed suspension, the ball pin of the hinge connected to the stabilizer must occupy a neutral (centered) position – this is the only way to achieve the maximum life of the stabilizer strut. With constant work in a state of maximum deflection angle, the destruction of the hinge is possible – the finger will pull out of the holder.
Ball joints
It would seem that it is difficult to pierce here. However, mistakes happen when installing ball joints.
Landing in a disposable lever. Many manufacturers produce assembled levers with SHO, without the possibility of a separate replacement of the latter. For some types, replacement is still possible with the use of special supports and special technology. FEBEST produces special ball bearings for replacement in aluminum and steel levers. Strictly observing certain technological operations when installing them.
Unfortunately, common practice is still to repress unsuitable SHOs into levers not intended for this. Often even with the use of welding. This practice is unacceptable. Since during welding, the body of the ball and polymer insert becomes mishapen, after which the support will not last for a long time.
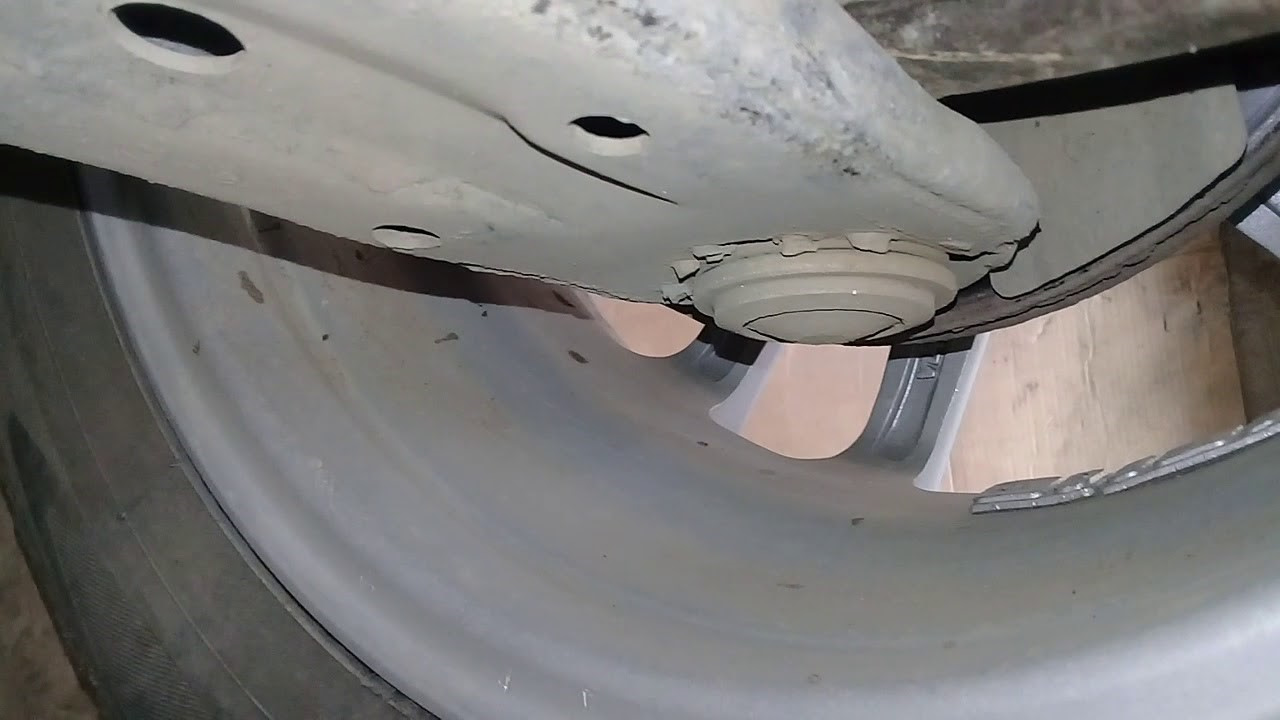
Shock absorbers
The internal construction of the shock absorber is of parts that are a precise match. So when installing new MacPherson struts or conventional shock absorbers, avoid the common mistakes.
1. Padding of the upper nut of the MacPherson strut struts. With excessive tightening force, the correct operation of the strut support is disrupted. The overtightened support bearing rotates with difficulty, which the driver often does not notice (due to power steering/EUR). Rapid wear of the support leads to knocking and failure.
There are also cases when, due to excessive tightening of the nut, the thread on the stem is pulled out. This leads to the rapid destruction of the threaded part of the stem, and it “flies away” into scrap metal.
2. Tightening the nut without fixing the stem. To install the racks, you use a special tool. It is a key that fixes the stem from turning when the nut is tight. If the rod is not fixed, ring marks from the piston may appear on the inner surface of the cylinder. These ring marks will lead to rapid wear of the rack. In some cases, using an impact wrench can loosen the stem’s inner nut, causing the shock to fail. Always tighten the shock absorber nut by hand and use the special tool.
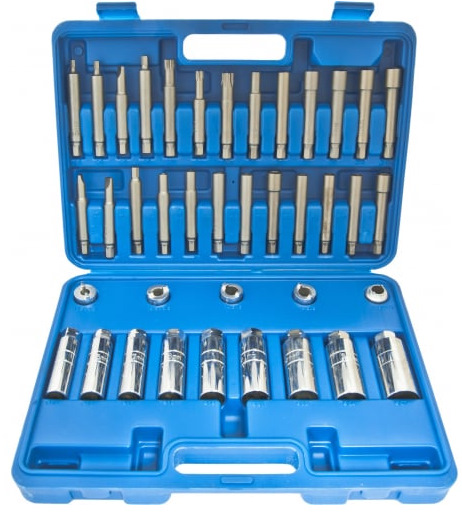
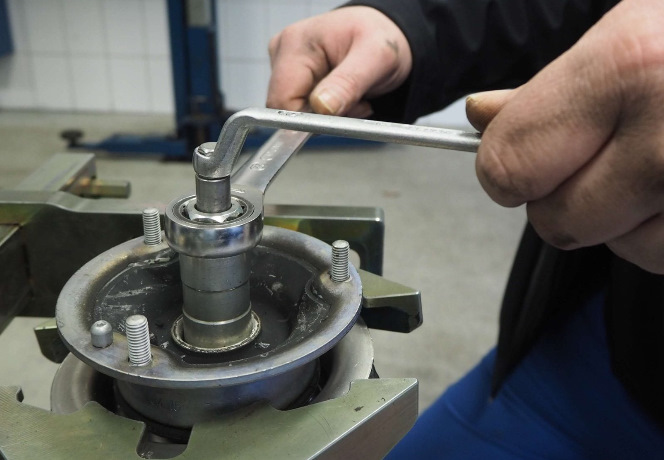
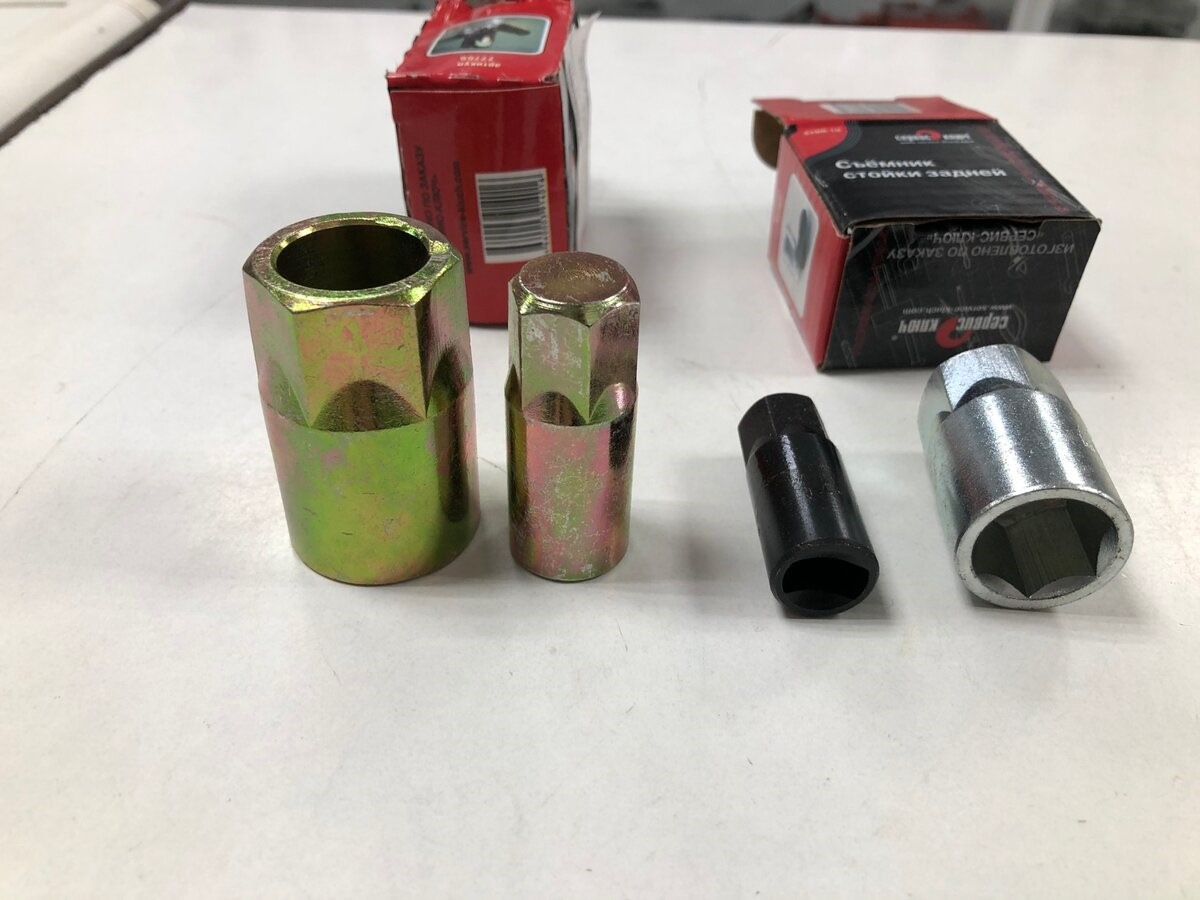
In Conclusion
Compliance with the rules when installing new suspension parts is the key to their reliable and long-term operation. When analyzing complaints, FEBEST specialists revealed that a significant proportion of suspension components fail prematurely. They are failing prematurely precisely because of errors made during installation.
Careful study of the manuals and the use of a suitable tool, will extend the life of the suspension and its components. And if you need repair and replacement, refer to the FEBEST electronic catalog . With hundreds of articles of silent blocks, stabilizer struts, and ball joints for cars of various makes and models listed.
Leave a Reply